Cooling socks, agricultural fabric and reflective yarn are a few examples of the innovative products developed by Wilson College of Textiles students during the Senior Design capstone course.
Each year, all seniors majoring in either textile engineering or textile technology are assigned a two-semesters-long project by an industry sponsor, such as Under Armour or Hanesbrands, where they apply classroom knowledge directly to industry challenges.
Seniors utilize Wilson College resources including the Textile Protection and Comfort Center (TPACC), the Zeis Textiles Extension (ZTE) and numerous labs and facilities to collect data, create prototypes and test materials throughout the research and development (R&D) process.
On Senior Design Day, project groups present their findings, offering in-depth research and creative solutions to industry leaders. Below, projects are sorted by category where teams explain their assigned challenge and conclusions.
Apparel textiles
Three-Layer Fleece
Sponsor: Hanesbrands
- Alex Crandall: Textile Engineering
- Will Dobrowski: Textile Engineering
- Jacob Haddock: Textile Engineering
- Jonah Nus: Textile Engineering
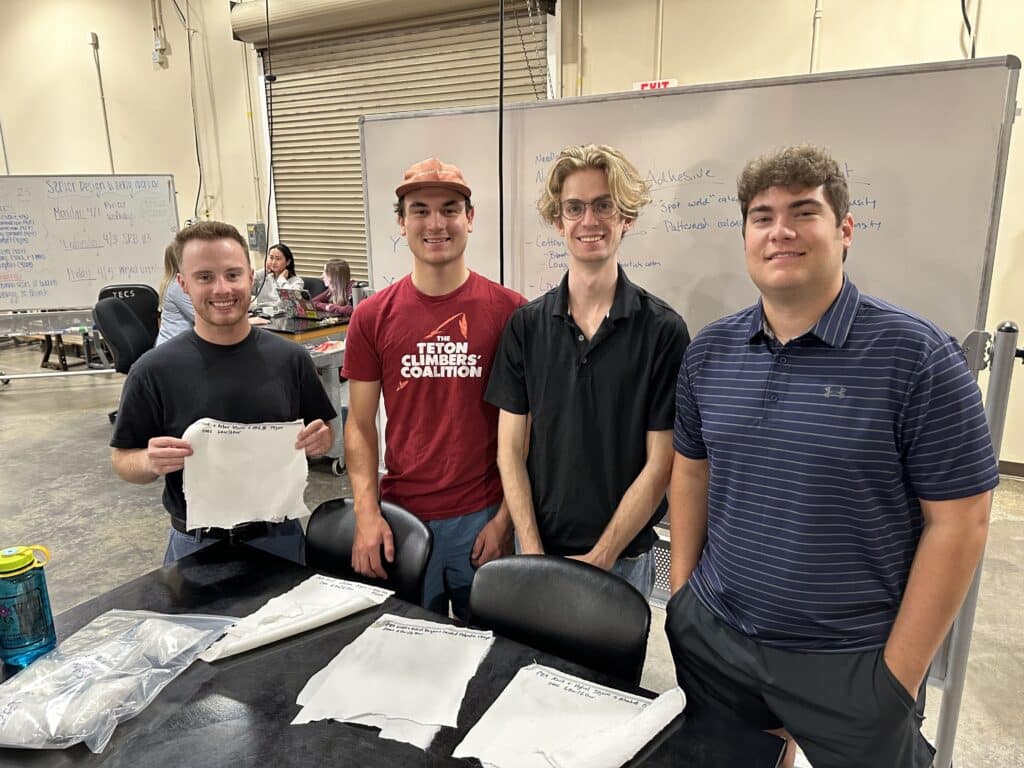
What was your challenge / prompt from your sponsor?
To create a new and innovative fleece material to compete with new products in the fleece hoodie market.
What types of tests / prototypes did you run and why?
We utilized both the knitting and nonwoven labs to produce our fleece fabric and the dyeing and finishing lab to help with prototypes, including carding, sanding and calendaring. For testing, we utilized TPACC as well as the tensile tester and the abrasion tester within the Wilson College. These tests helped us to quantify our design choices, improve our fabric and assist in the production of our final prototypes.
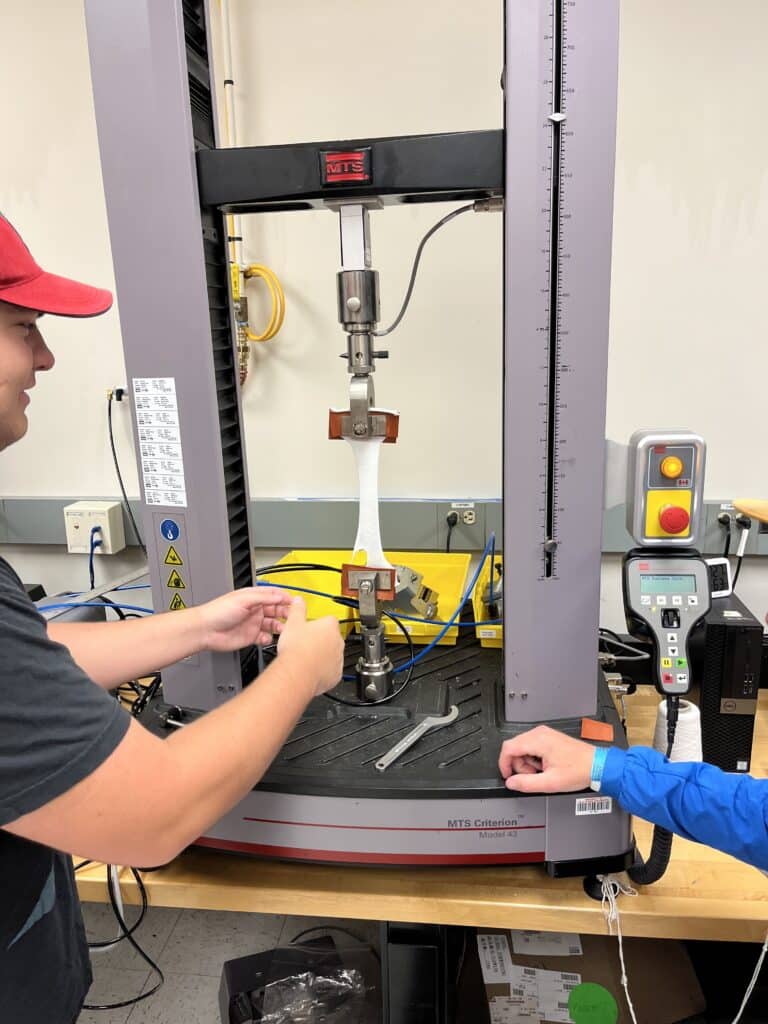
What did you come up with? What was the solution, end product or process that you are presenting?
We developed a three-layer fleece material which includes a knit outer layer, an elastomer adhesive and a non-woven skin-facing layer to provide warmth and a soft feel. This allows us to produce a warmer, stronger and better-looking fabric compared to fully nonwoven garments.
Cooling Socks
Sponsor: Hanesbrands
- Kylie Scott: Textile Technology
- Tytianah Ward: Textile Engineering
- Kinkead Crotts: Textile Engineering
- KJ Crenshaw: Textile Technology
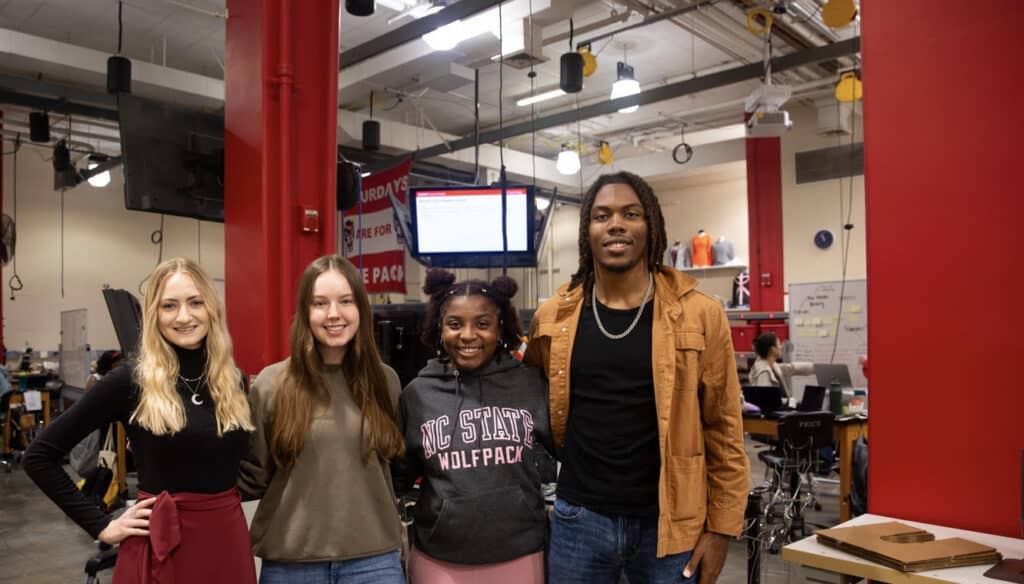
What was your challenge / prompt from your sponsor?
Hanesbrands tasked our team with creating a sock that is physically cool to the touch and can help regulate the temperatures of a person’s foot, keeping the wearer cool and comfortable all day long.
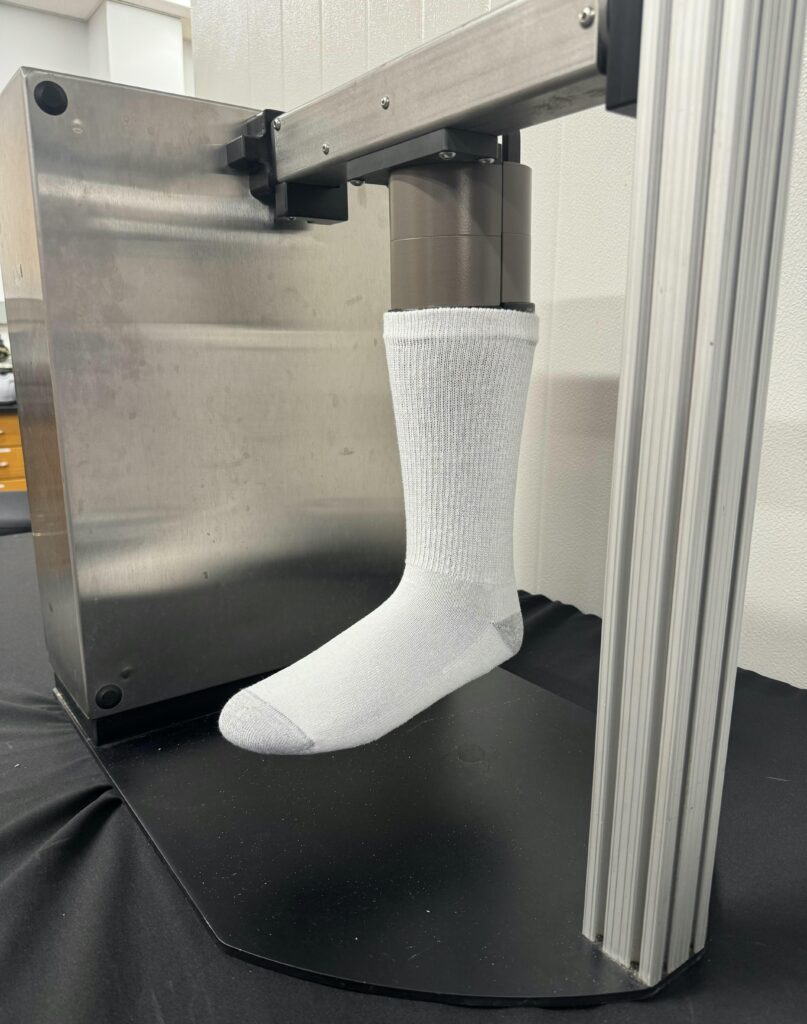
What types of tests / prototypes did you run and why?
The two main tests we ran were the Qmax warm/cool touch test and a thermal insulation test using the sweating foot manikin system in TPACC. The Qmax test measured the initial cool to the touch feel of the fabric by measuring the transient heat transfer that occurs the first time the fabric contacts the skin. Thermal insulation was tested to evaluate the heat and moisture management of the footwear system.
We tested five socks available on the market today to get a baseline of existing products. In addition, we tested seven different yarn types and three blends to determine what performed the best. These tests allowed us to see how cool the sample is on initial contact and how much body heat is allowed to escape.
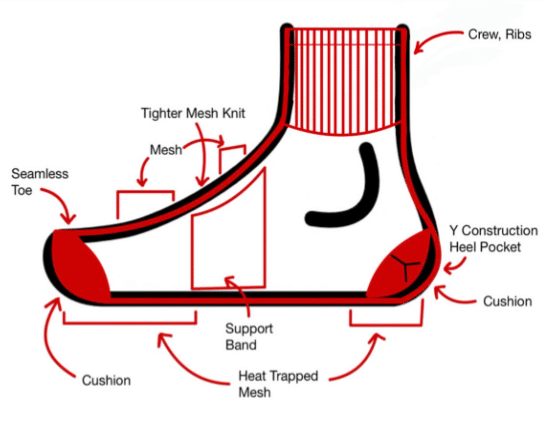
What did you come up with? What was the solution, end product or process that you are presenting?
Based on the large amount of research and testing that we did, our current solution is a sock made from bamboo rayon. Bamboo rayon has very high thermal conductivity and responsivity and performed very well in both Qmax and thermal insulation testing.
Sustainable Textiles
Monomaterial Garments
Sponsor: Hanesbrands
- Madison Murry: Textile Engineering
- Henry Phillips: Textile Engineering
- Julia Heilmann: Textile Technology
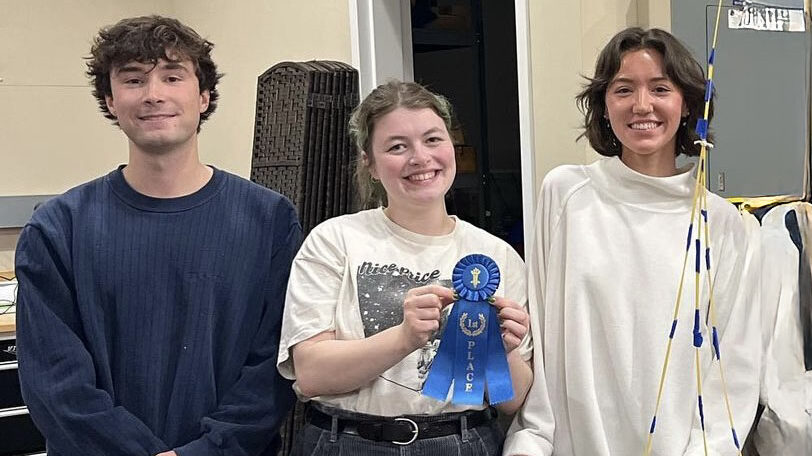
What was your challenge / prompt from your sponsor?
Our team was tasked with creating a garment entirely out of one material, including all seams and other components such as zippers, grommets or elastic. The purpose of creating a garment out of a singular material is to ease the process of textile recycling.
Fiber sorting is the most labor intensive process within textile recycling, costing millions of dollars in equipment and skilled workers. Monomaterial garments can bypass this process and be directly recycled as a whole garment. Not only does this save time and money, it also reduces the amount of waste that ends up in landfills from the non-recyclable components of these deconstructed garments.
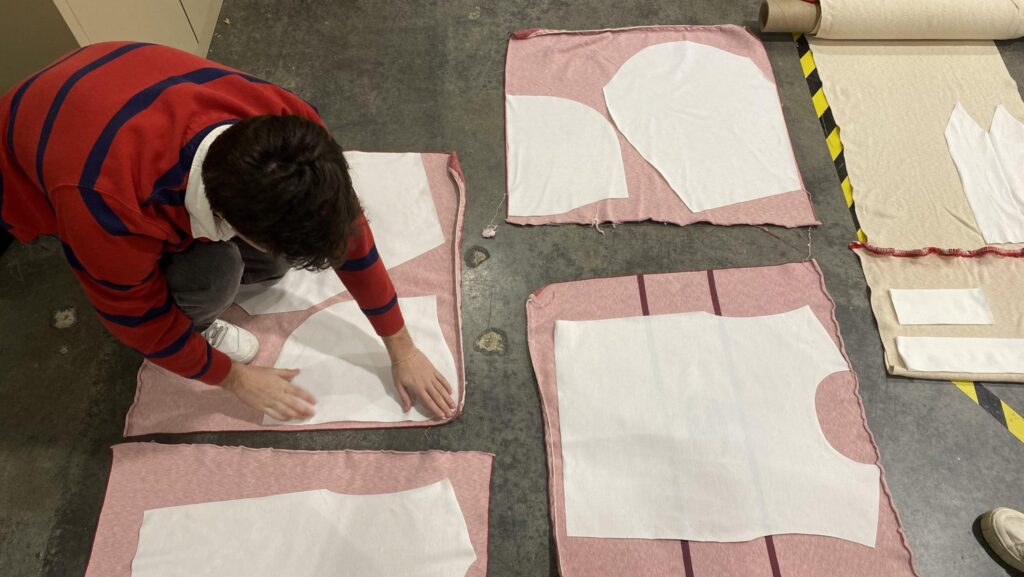
What types of tests / prototypes did you run and why?
The most important tests we had to run were for thread and seam strength. We had to test that our 100% cotton thread held up to today’s industry standard of cotton-polyester thread. After this, we sewed the selected thread in several different seam types and tested the strength of each seam to compare against Hanes and Champion hoodie seams. Beyond strength, we also tested our 100% cotton fabric for flammability, air permeability, pilling and abrasion resistance.
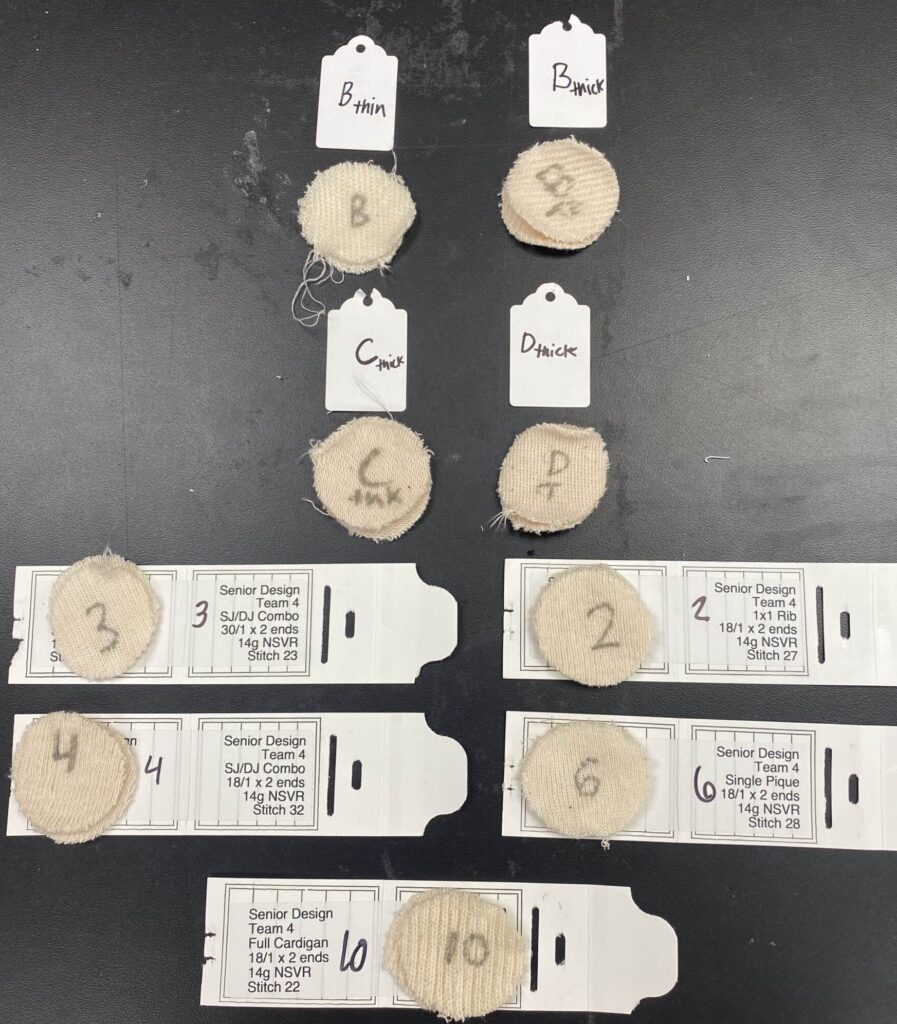
What did you come up with? What was the solution, end product or process that you are presenting?
We ended up creating two garments, both made from 100% cotton but with very different use cases. The first garment is a heavy-weight hoodie designed for maximum warmth. This garment consists of a full Jacquard body panel, 1×1 rib knitting along the sides for breathability and comfort and a shortened waistband and cuffs. The other garment is a flowy sweatshirt made mostly from a terry fabric. It has a mock neck and overall a very loose construction for maximum comfort.
What was your favorite / most interesting thing you learned about your subject area?
We all really enjoyed getting to go through the entire product development process. We started with a very open prompt and to see our visions come to fruition with these garments is something we are very proud of.
Natural Dye Impact
Sponsor: Under Armour
- Brandon Russ: Textile Technology
- LeeAnna Hines: Textile Technology
- Drew Lingerfelt: Textile Engineering
- Kairas Williams: Textile Engineering
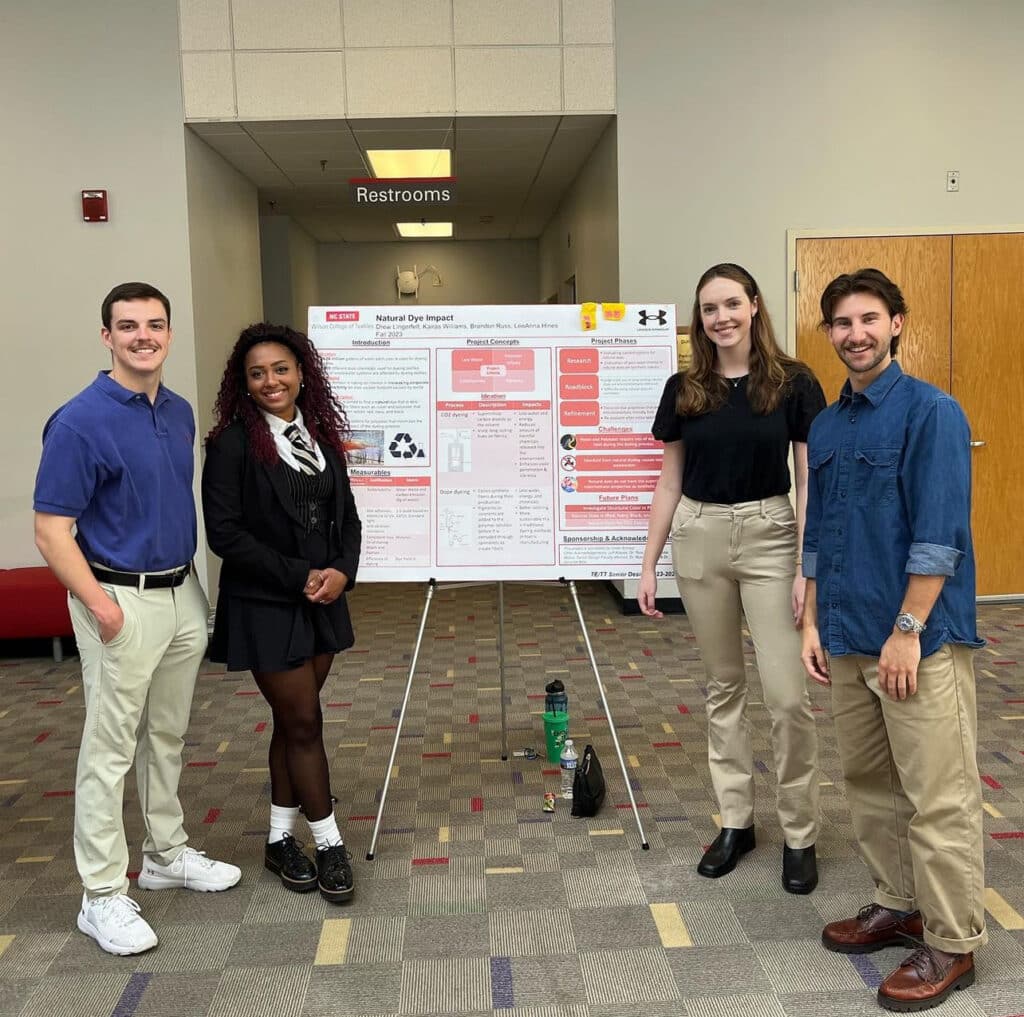
What was your challenge / prompt from your sponsor?
For our Senior Design project, we were tasked by Under Armour to evaluate natural dyeing options for polyester that minimize the negative environmental impact of the dyeing process.
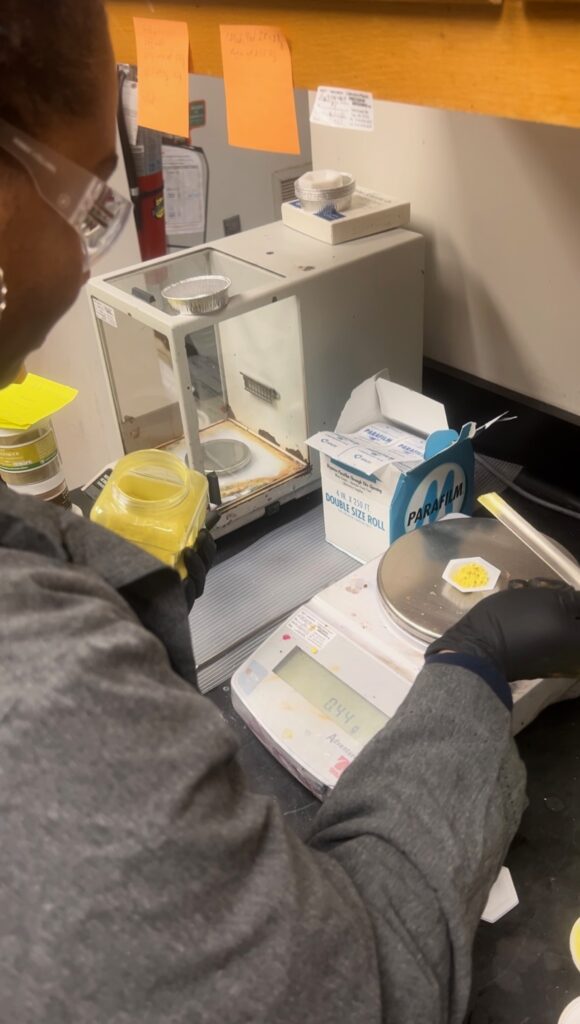
What types of tests / prototypes did you run and why?
We experimented with different additives, processes, temperatures and concentrations of dyes. We tested wash fastness, crockfastness (how much does color transfer from the garment) and light fastness on our prototypes to evaluate how well the natural materials dyed the polyester fabric and resisted fading. To complete these tests, we used the Ahiba Datacolor machine, crockmeter, spectrophotometer, laundering machine and lightbox.
What did you come up with? What was the solution, end product or process that you are presenting?
Starting with 20 dyes, we experimented with different variables of dyeing, including additives and temperature. Our group was able to come up with eight different dyes that fit our project criteria as follows: Marigold (yellow), Madder Root (yellow), Cape Jasmine (blue), Gardenia Blue (blue), Old Fustic (brown), Gambir (brown) and Mulberry Leaf (green).
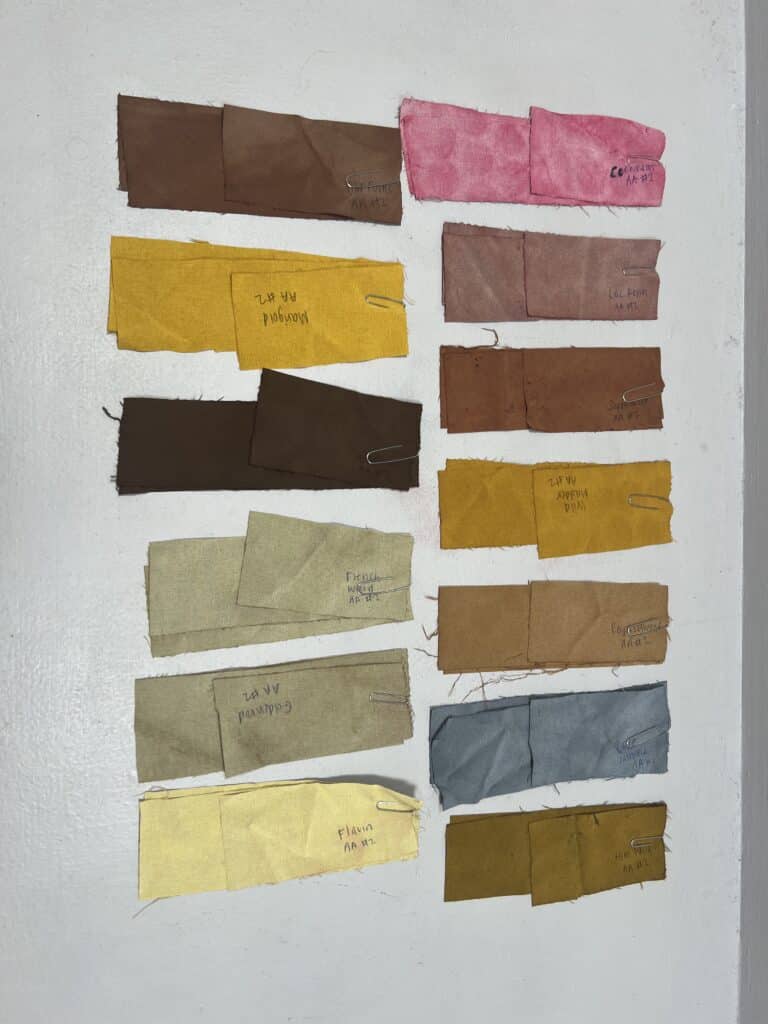
What was your favorite / most interesting thing you learned about your subject area?
The most interesting piece of our project was discovering how many natural dyes are available. During our preliminary research we had to spend time narrowing down which dyes we wanted to experiment with.
Net Zero Carbon Hoodie
Sponsor: Hanesbrands
- Rachel Falkowski: Textile Engineering
- Ysa Ferreria: Textile Technology
- Colin Kirila: Textile Engineering
- Yuchen Zhou: Textile Technology
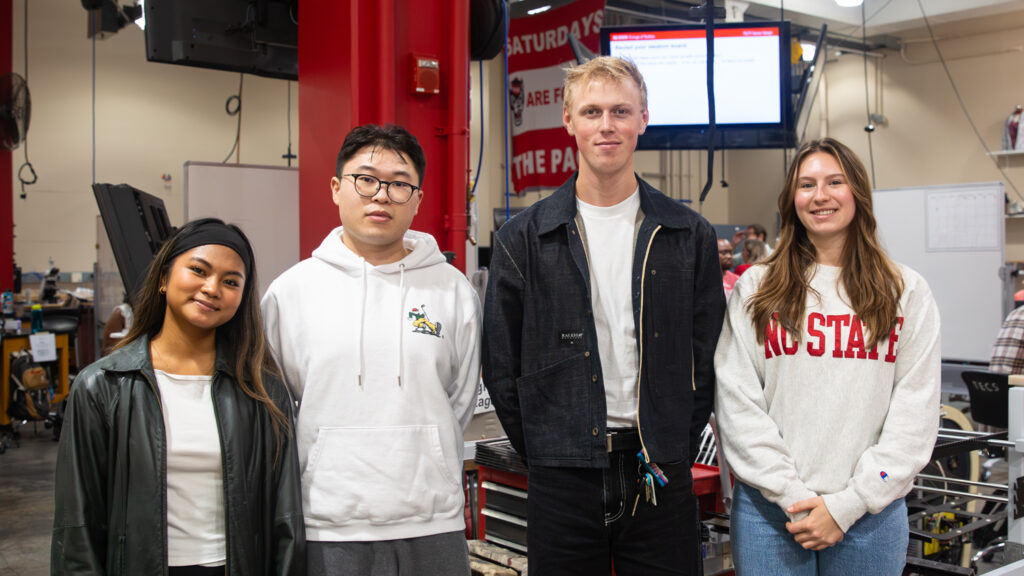
What was your challenge / prompt from your sponsor?
Create a net zero carbon hoodie. Net zero carbon means the amount of CO2 produced is equal to the amount of CO2 removed from the atmosphere.

What types of tests / prototypes did you run and why?
Supercritical CO2 dyeing was used to test a more sustainable dyeing method with natural dyes. We created three separate “net zero” hoodie prototypes with sustainably focused hang tags. We also generated a sustainability campaign focused on educating shoppers on cold washing and hang drying. We created our own logo, embroidered it directly onto the hoodie and created our own back tag that we will be screenprinting onto the hoodie.
What did you come up with? What was the solution, end product or process that you are presenting?
We came up with a final hoodie prototype that reduced unnecessary fabric usage, incorporated more sustainable dyeing methods and generated a tree-planting campaign. All of these individual tasks add up to a final product that is “net zero.”
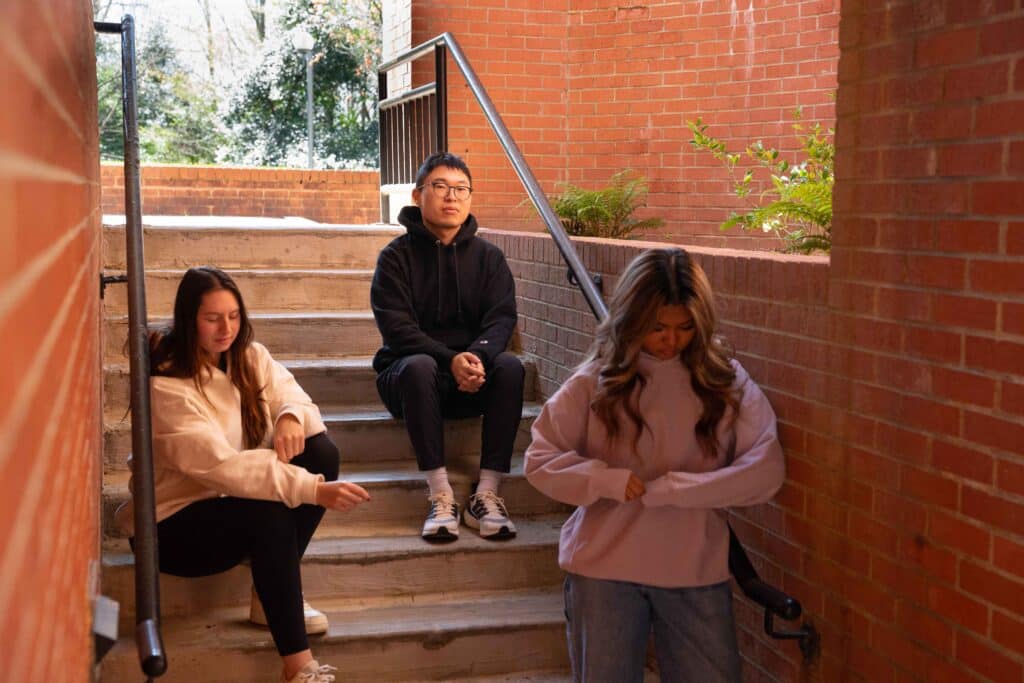
What was your favorite / most interesting thing you learned about your subject area?
One of the most valuable points we took away from this project was learning how emissions data is calculated. Creating a full life cycle assessment for one product is not typically done. We had to go through each of the hoodie manufacturing processes and pull data. This allowed us to get a broader understanding of how emissions data is calculated in all aspects of garment production.
Reusing Sails
Sponsor: Sail to Shelter
- Charlotte Willis: Textile Technology
- Kaleah Gaddy: Textile Technology
- Ashwaath Sathyanarayanan: Textile Technology
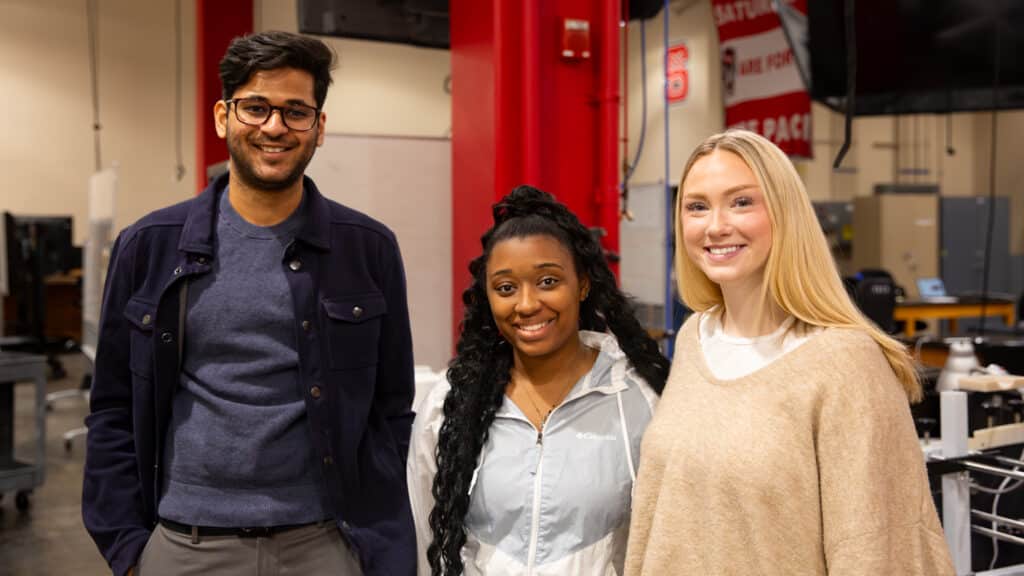
What was your challenge / prompt from your sponsor?
We had a pretty open prompt but the general goal our sponsor had in mind for us was to find a useful way to reuse or repurpose old sailboat sails.
What types of tests / prototypes did you run and why?
We ran Fourier Transform Infrared (FTIR) Spectrometer tests to identify what the sails were made of so we could figure out what the expected performance of the sails would be, how we could reuse them and if it would be possible to break them down for recycling or another use.
For our prototype, we outsourced perforation to IPS Perforation where they essentially punched 1.5mm holes into our recycled sails for water drainage. The goal was to create an agricultural fabric to prevent weed growth. We used the Senior Design Lab and the Physical Testing Lab to run tensile tests, moisture management tests and water repellency tests. We ran these to evaluate the performance of our industry-standard fabrics and our prototypes.
What was your favorite thing / most interesting thing you learned about your subject area?
One of the most interesting things we learned about was how much waste the sailing industry produces. None of us had any experience in sailing or know really anything about sailing as a sport so getting to do research into the industry and how much waste it produces has been astounding.
Reusable Novel Core for Menstruation and Incontinence Underwear
Sponsor: Procter & Gamble
- Rosie Fisher: Textile Engineering
- Liz Siu: Textile Engineering
- Zimeng Li: Textile Technology
- Maddy Moore: Textile Technology
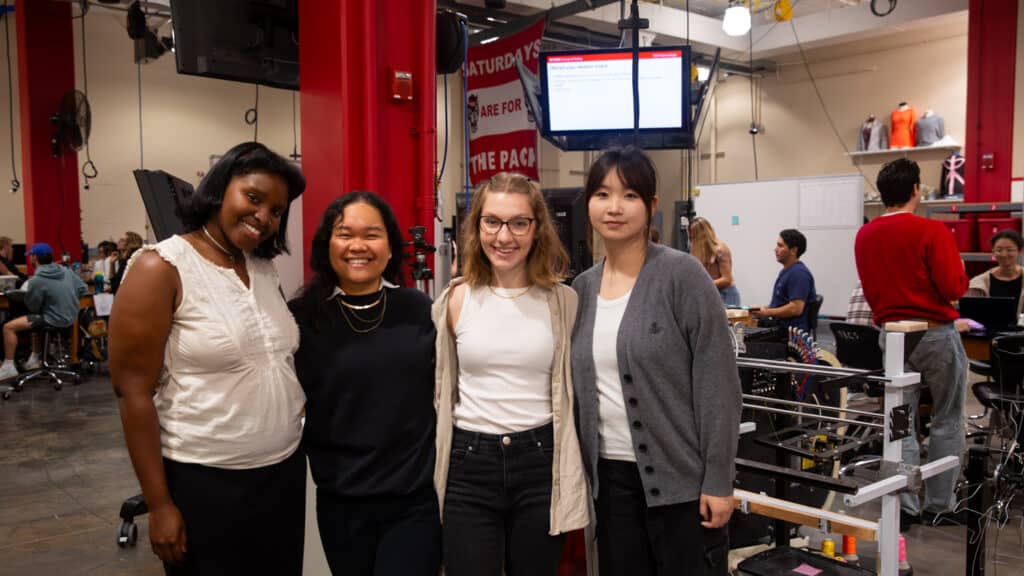
What was your challenge / prompt from your sponsor?
To create a high absorbency novel core for reusable menstrual and incontinence underwear that is thinner than current products while maintaining dryness and capacity.
What types of tests / prototypes did you run and why?
We made yarn for some of our prototypes in the prototyping lab, knit prototypes in the Knitting Lab and finished samples in the Dyeing and Finishing Lab. We tested our industry standard materials and prototypes for thickness in the Physical Testing Lab, did moisture management testing in the Senior Design Lab and tested for capacity and dryness with methods we developed in the Undergraduate Research Lab. We also made our own simulated blood to test with and verified its viscosity with our new viscometer in Senior Design.
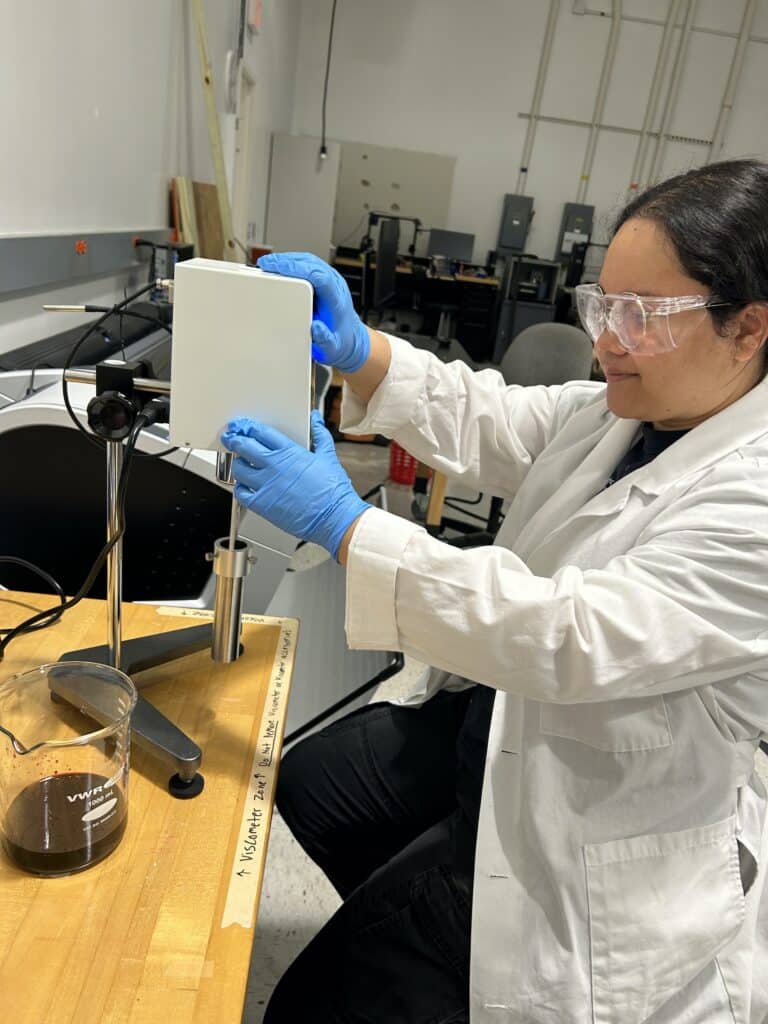
What did you come up with? What was the solution, end product or process that you are presenting?
Our main project goal was to innovate a novel core for reusable menstrual and incontinence underwear that was thinner than current products while maintaining the same levels of dryness and capacity. A secondary goal was to decrease the rinse time for the user after they are done wearing the underwear.
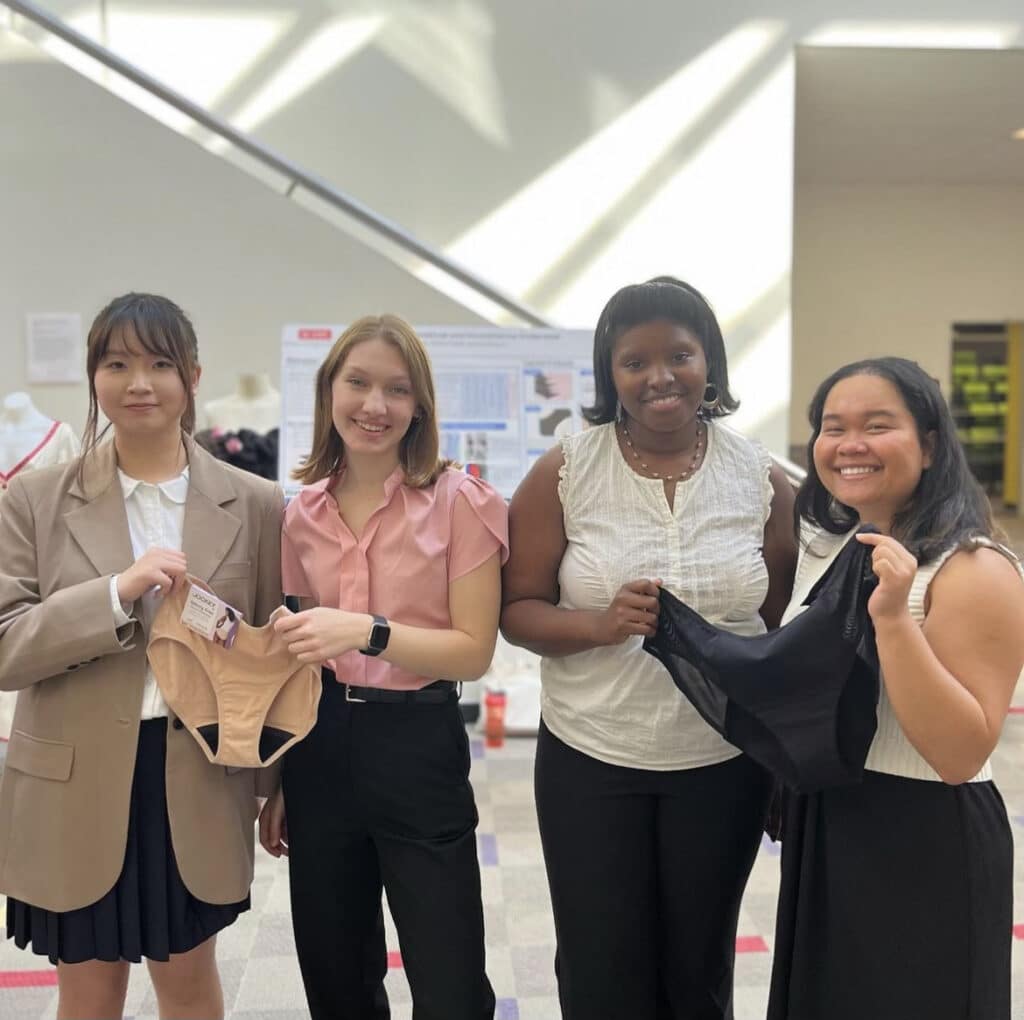
Where / how do you think you’ll apply the knowledge you have developed in Senior Design?
The skills and knowledge we developed in Senior Design will definitely help us as we continue our careers. Engineering and technology are very collaborative fields, so working on a year-long project with a team allowed us to learn from one another and gain experience with project management, delegation, collaboration and lots of problem-solving!
Athletic and performance textiles
Rub on E-Textiles
Sponsor: Advanced Functional Fabrics of America
Team members:
- Leo Delgado: Textile Engineering
- Peighton Jones: Textile Technology
- Carlos Alonzo-Montufar: Textile Engineering
- Paige Greener: Textile Engineering
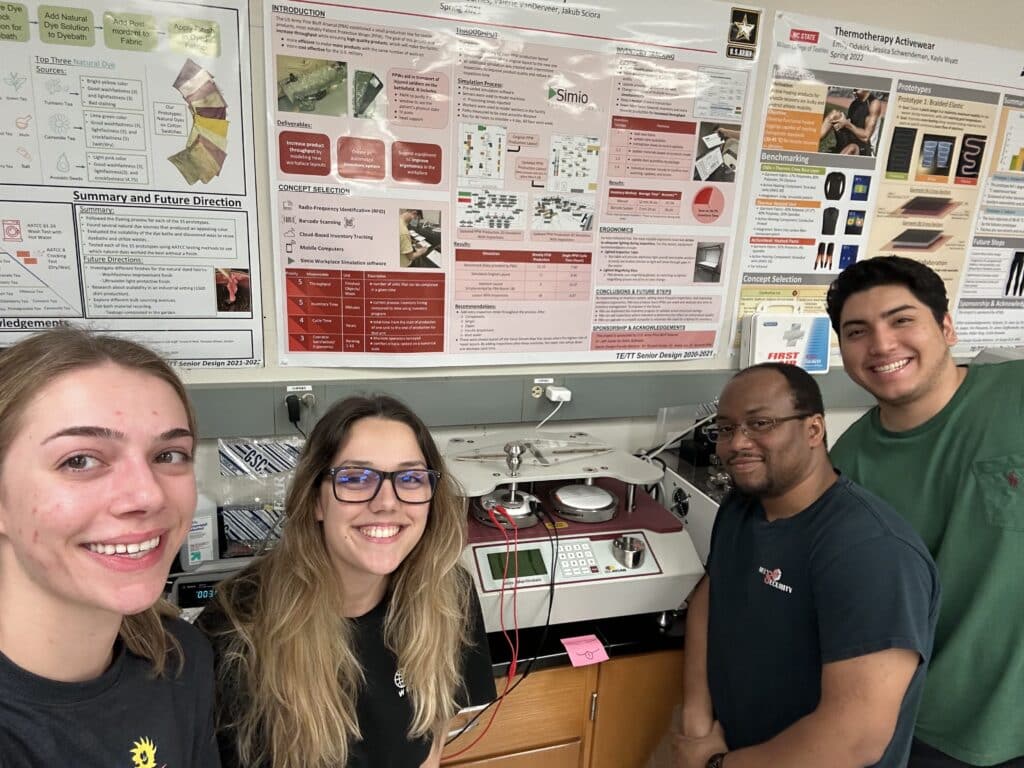
What was your challenge / prompt from your sponsor?
In this project, our design team collaborated with the Advanced Functional Fabrics of America (AFFOA) technical team to develop a new method for testing electronic textiles (e-textiles).
We were assigned the task of devising a standardized abrasion (damage and wear) test method for textile-based data and power conductors, aiming to gain insights into their durability. This included the development of a standard operating procedure and the necessary statistical data analysis to ensure the reliability and reproducibility of the test method.
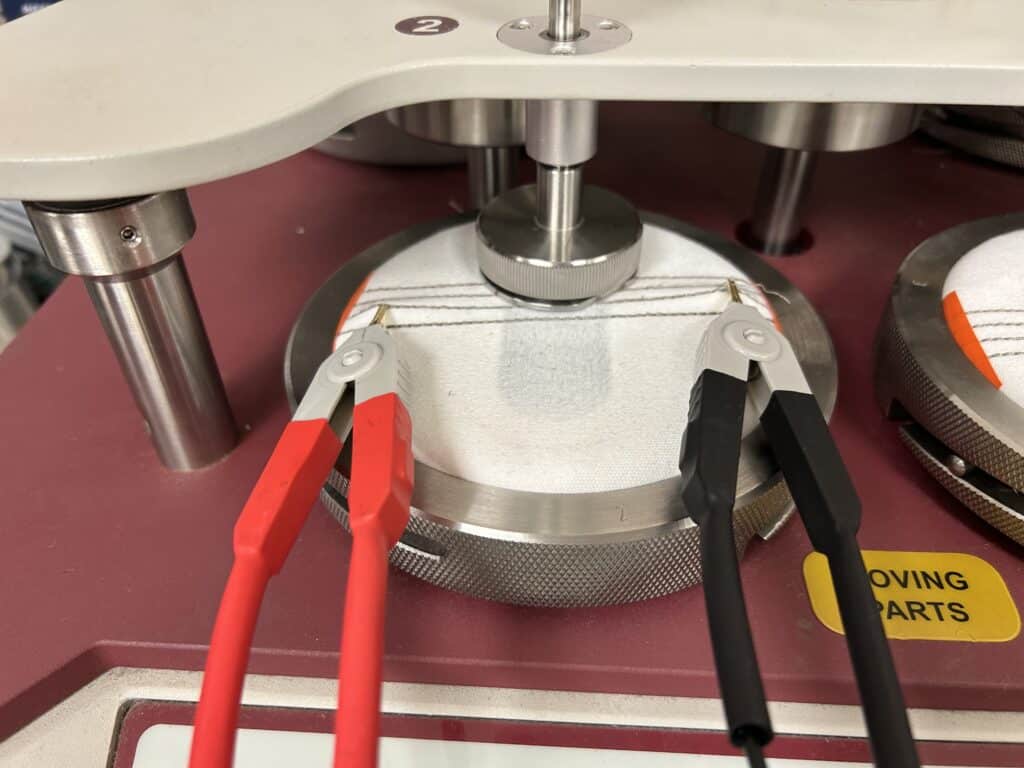
What types of tests / prototypes did you run and why?
To validate our developed test method, we utilized prototypes such as screen-printed and embroidered e-textiles created by the team and AFFOA. The objective was to create a standardized method to investigate the abrasion resistance, change in electrical resistance and changes in the appearance of e-textiles. We employed Martindale abrasion test methods adhering to various industry standards. Additionally, we conducted a Gauge R&R study to assess the reliability and reproducibility of our test method.
What did you come up with? What was the solution, end product or process that you are presenting?
We developed an abrasion test method following standards similar to existing industry standard tests. However, we modified the abrasion test to include measuring and collecting data related to the electrical resistance of the e-textile sample while undergoing the Martindale test. In addition, to facilitate the measurement of electrical resistance, we reversed the positions of the abrasive material and the sample, with the sample placed on the bottom and the abrasive material on the top.
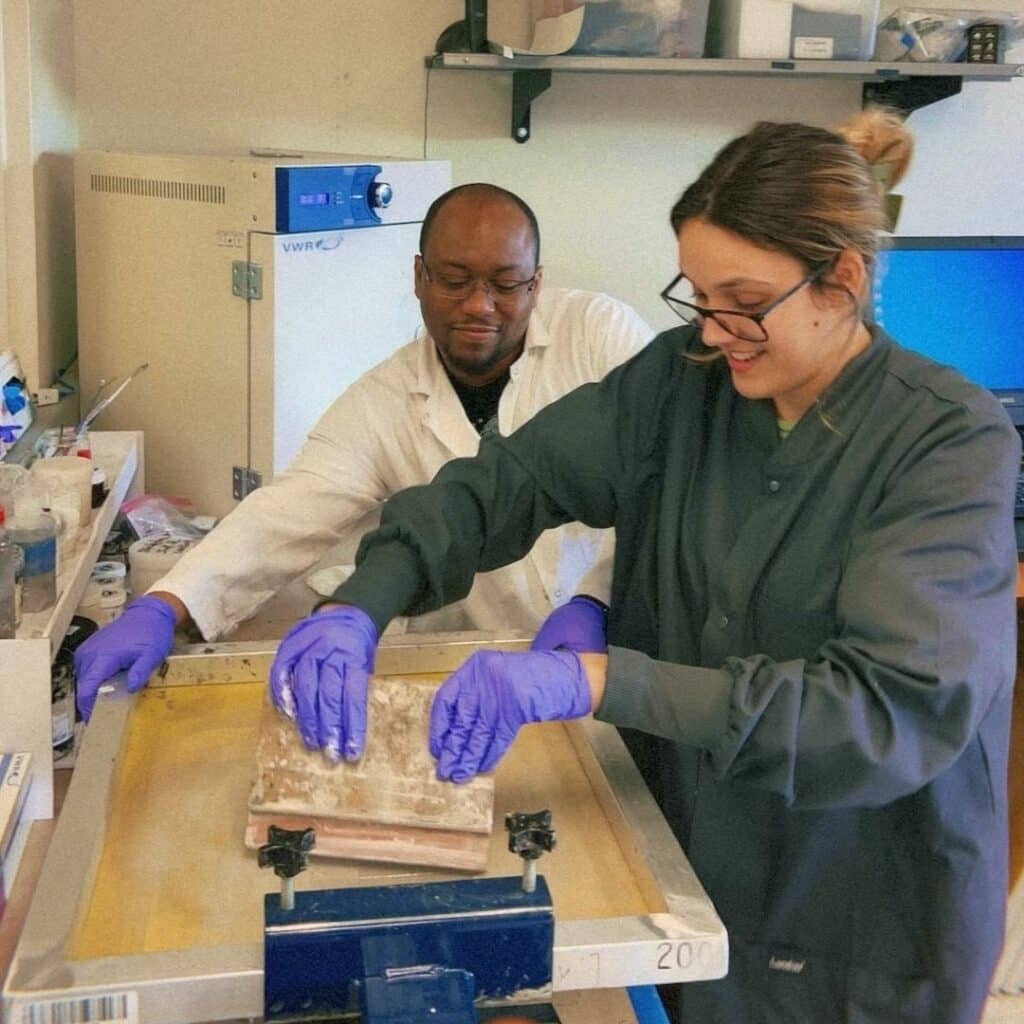
What was your favorite / most interesting thing you learned about your subject area?
Given our team’s initial limited experience with e-textiles and electronics, our favorite aspect of the project has been our collaborative journey towards a common goal while delving into new territory. Throughout the project, we embraced the challenge and enjoyed learning new things such as screen printing, Arduino programming and test method development. The opportunity to collaborate and learn together while discovering an unfamiliar field of textiles has been a very rewarding experience.
Natural Fiber Welding
Sponsor: American & Efird
Team members:
- Brigitte Gallagher: Textile Engineering
- Colleen Sheridan: Textile Technology
- Jenna Diemel: Textile Engineering
- Logan Boyle: Textile Technology
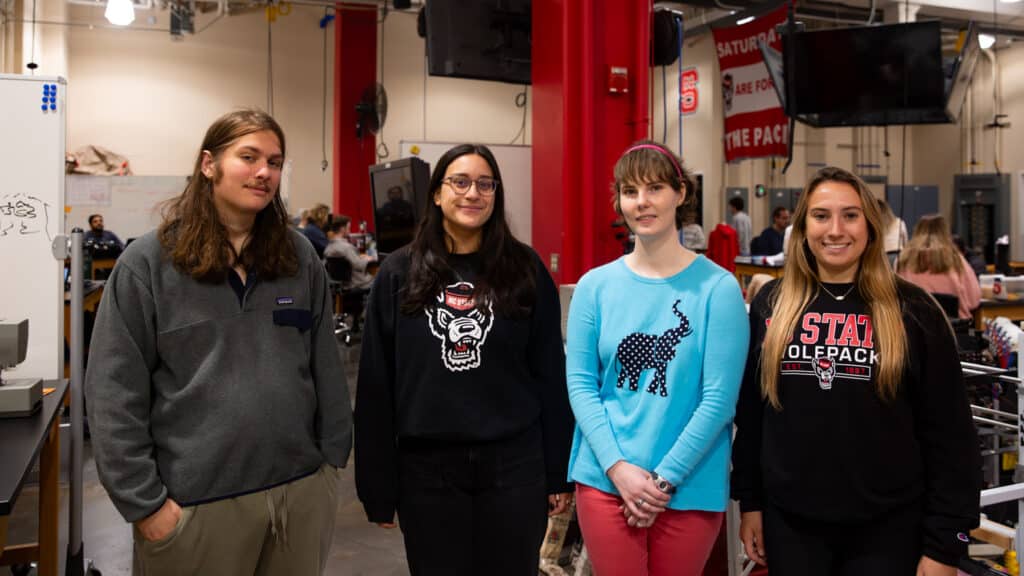
What was your challenge / prompt from your sponsor?
We assessed the mechanical performance of 100% long-staple cotton yarns that had been treated with the Clarus process. The process claims to improve the strength of cotton yarns. We also looked at the mechanical properties of the yarn after dyeing and overdyeing.
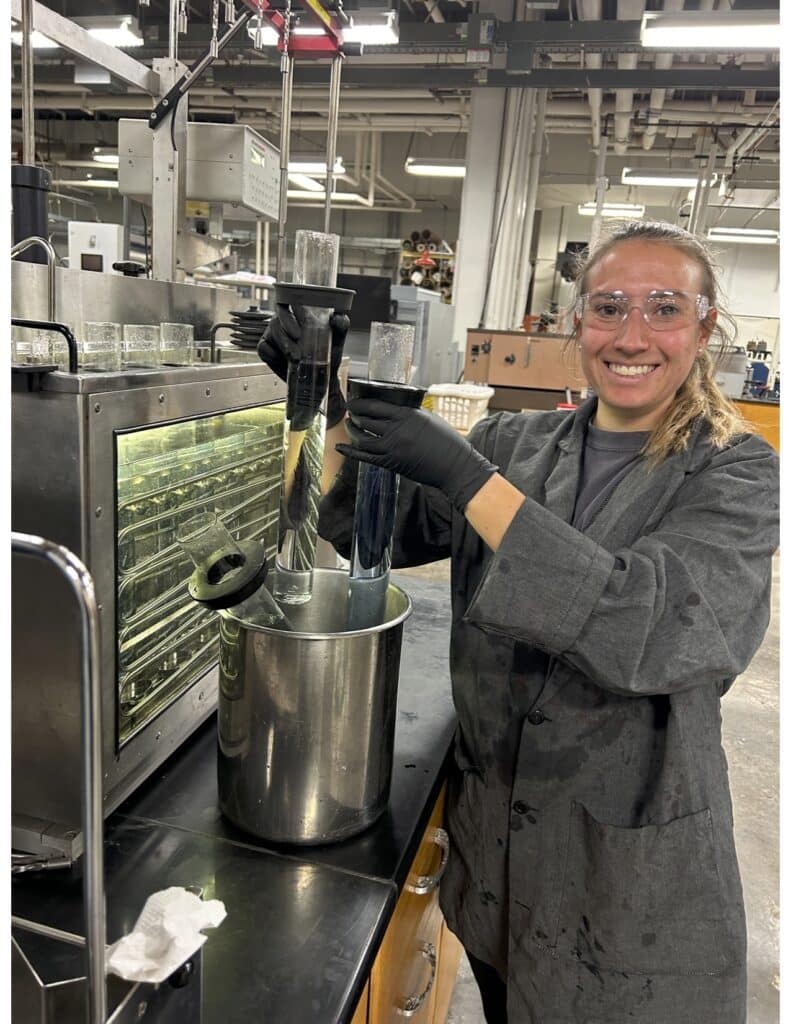
What types of tests / prototypes did you run and why?
We evaluated the mechanical and chemical properties of a 30/2 Pima cotton thread called Anecot Plus before and after a chemical welding process was applied. Our samples were an untreated Anecot Plus, a light weld Anecot Plus and a medium weld Anecot Plus.
We assessed strength, elongation, diameter and dyeability. We did this by evaluating the tensile properties of the threads by themselves at each dye stage, as well as their seam strength as both greige (unfinished) and overdyed threads. The individual thread properties were obtained via Uster Tensorapid, while the seam strength was found through an MTS criterion tester.
In our dye trials, we utilized the Ahiba Texomat to perform dyeing using reactive blue and then reactive read dye trials at one and three percent shade respectively. We also analyzed the dye performance at each stage for each sample using a spectrophotometer. This machine provides us with the actual shade and hue of a given sample, which we can use to compare them. We also found the diameter and hairiness values for the greige samples, so the original impact of the weld could be determined.
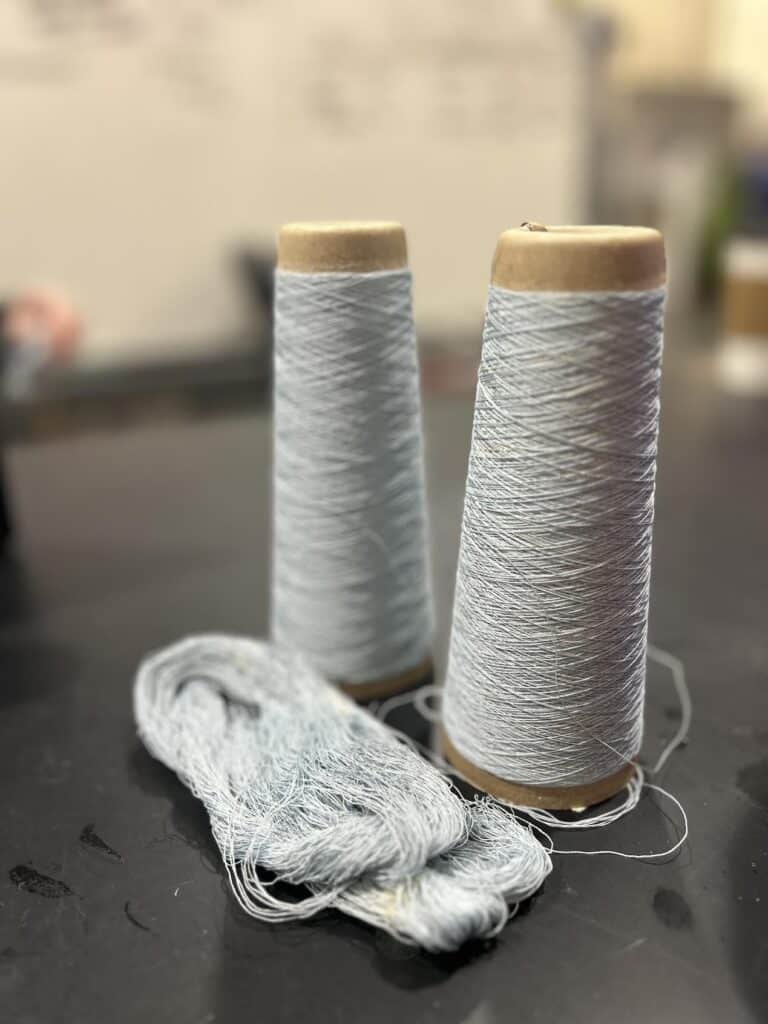
What did you come up with? What was the solution, end product or process that you are presenting?
On Design Day we used yarn boards, cones and skeins of samples to provide a visual and tactile representation of our data. There was free skein of each for our audience to freely manipulate the sample. The yarn boards and cones provided a better view of color and actual yarn geometry.
What was your favorite thing / most interesting thing you learned about your subject area?
Learning about the chemical welding process created by Natural Fiber Welding. NFW uses Clarus technology to fuse natural fibers and increase strength properties. This technology was made with the goal of sustainability in mind, so being a part of its early testing and conception was very rewarding.
Redesigned Reflective Yarn
Sponsor: Under Armour
- Seongjin Kim: Textile Engineering
- Megan Mae Dingle: Textile Engineering
- Sam Pan: Textile Technology
- Victor Alvarez Valverde: Textile Technology
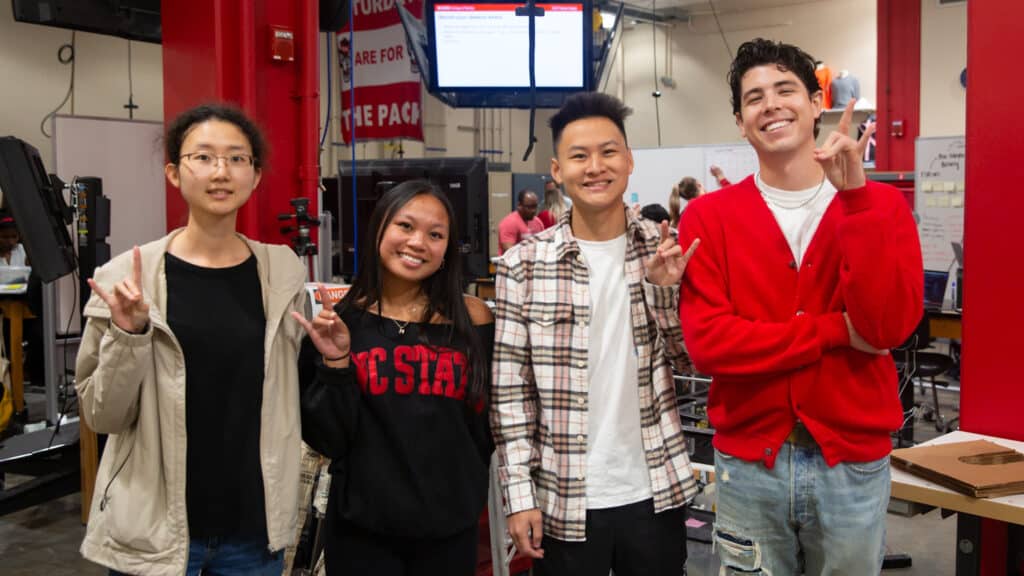
What was your challenge / prompt from your sponsor?
Our challenge was to redesign reflective yarns. With 76% of pedestrian accidents occurring at night, reflective yarns provide safety for athletes looking to play sports or train at night. Current available yarns are either highly reflective but uncomfortable or very comfortable with little reflectance, so we were tasked with maximizing both the reflectance and comfort of a yarn.
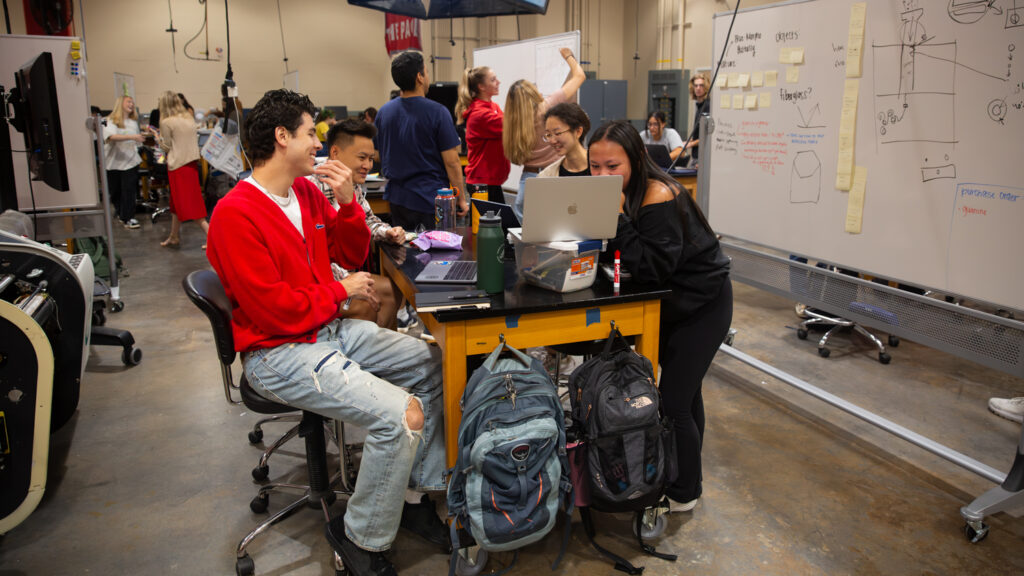
What types of tests/prototypes did you run and why?
The scanning electron microscope (SEM) was used to see the surface morphology and structure of our reflective benchmarks. We used Hitachi TM4000 in the SEM and Forensic Testing Microscopy Laboratory in the Wilson College.
We conducted air permeability testing in the college’s Physical Testing Lab in order to to compare fabric breathability among different industry standard reflective materials.
What did you come up with? What was the solution, end product or process that you are presenting?
Our project focused on developing a polyester yarn with a reflective coated component. Ideation consisted of altering the cross-section of the yarn, applying coatings with various reflective materials and extruding a reflective yarn with reflective material integrated at a fiber level. Based on our prototyping and testing processes, the most suitable solution we found was coating the yarn with a binder, which improves mechanical properties, and then applying an aluminum-coated glass bead. This ultimately improved the hand of the yarn while maintaining the high reflectance values of glass and mirrors.
This post was originally published in Wilson College of Textiles News.