Textiles Senior Design Students Partner with U.S. Army, Under Armour
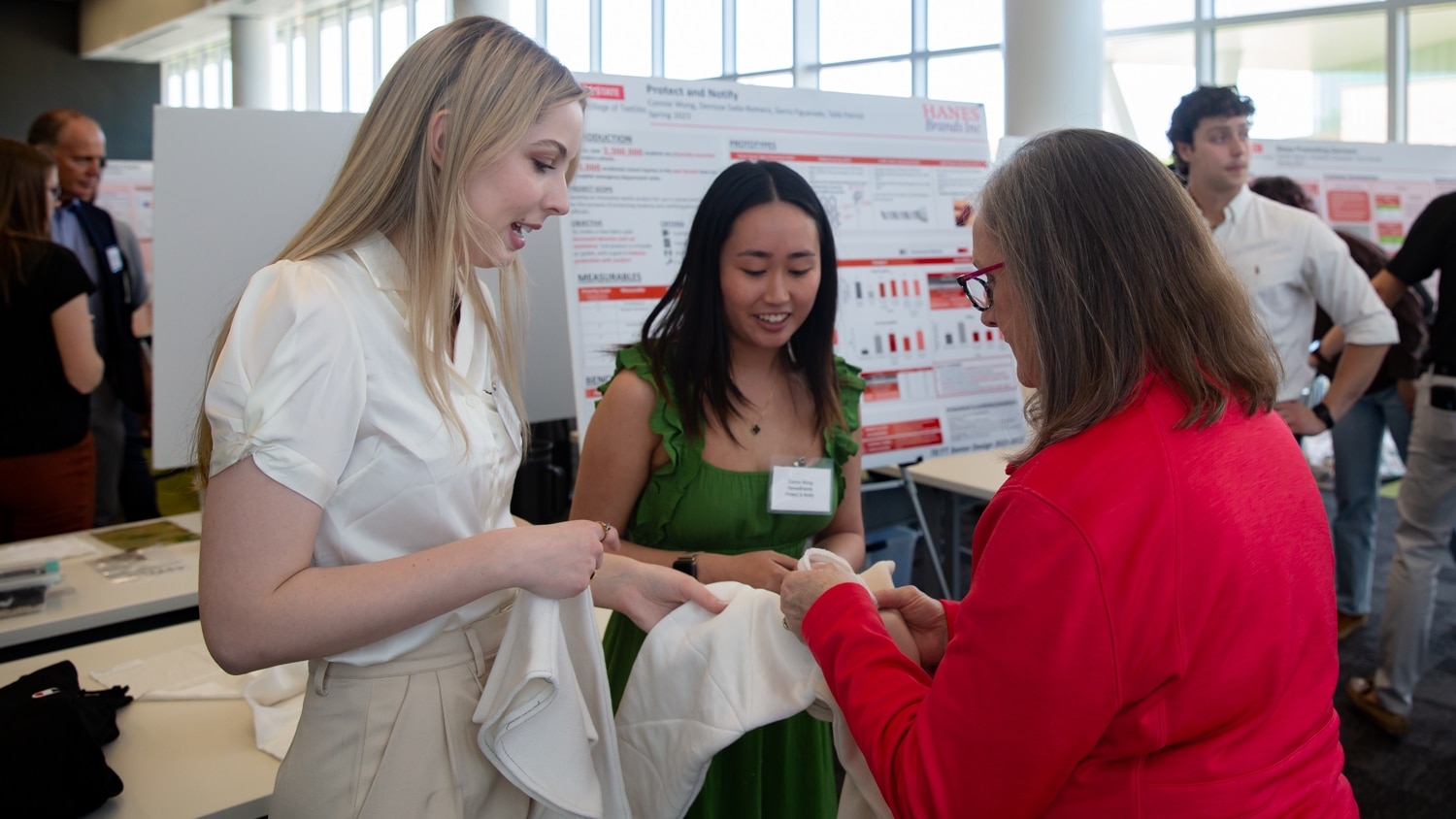
By Elyse Boldizar and Sarah Stone
A shelter made of sails otherwise destined for the landfill, a patient elevator, a more breathable pair of sneakers, a new base layer for U.S. Army uniforms: you can only find this collection of items at Senior Design Day for the Wilson College of Textiles.
Every year, seniors majoring in textile engineering (TE) or textile technology (TT) at NC State University team up with a few classmates, as well as industry partners, to address a real-world problem for their capstone course.
Over the course of two semesters, they gain hands-on experience in the research and development (R&D) process for process and/or product development.
“I think Senior Design has been so helpful, because we got to learn how to start with research and then go all the way through product development and prototype development,” TT alumna Connie Wong ’23 says.
Students are grouped into teams and assigned to projects based on their interests and leadership styles, helping to prepare these seniors specifically for the jobs they want post-graduation.

“I’m currently looking to work with hands-on testing after graduation. I feel like this project specifically has helped us focus a lot on that. And we’ve learned a lot about what testing requirements look like and we even had to learn how to modify existing tests,” TE alumna Lara Prosser ’23 says. She and her teammates worked to find a biodegradable fiber for use in U.S. Army uniforms. “I just feel like the more that I get to actually do hands-on testing, the more I realize just how fun it is.”
The job outcomes for this new class of alumni — from Nike to Lenovo to research labs — are a testament to the strength of the Senior Design program.
Below, read more about the range of projects these Senior Design groups worked on and hear about the impacts of those projects in their own words. Click one of the links below to filter Senior Design projects by topic.
- Military/protective textiles
- Medical/safety textiles
- Athletic/performance textiles
- Sustainable textiles
- Apparel textiles
Military/protective textiles
Team 9: Biodegradable Polymer Replacement
Sponsor: U.S. Army Combat Capabilities Development Command (DEVCOM)
Team members:
- Lara Prosser (Textile Engineering)
- Susie Richart (Textile Engineering)
- Jocelyn Zhu (Textile Technology)

What was your challenge/prompt from your sponsor?
Nylon still makes up a large portion of textile manufacturing in the Department of Defense. However, nylon has significant environmental impacts over its lifecycle. This starts with a toxic production process and ends with a material that is slow to degrade with a legacy of micro-polymer pollutants when it does.
Our team was tasked with finding a biodegradable polymer that would have similar degradation properties to natural fibers and the mechanical properties of nylon. We gathered information on the market, obtained and tested samples and compared the samples against nylon benchmarks.
What solution or end product did you come up with?
Our team proposed three polymer alternatives to nylon which have comparable mechanical properties and significant advancements in biodegradation. To do this, we utilized the Wilson College Spinning Lab, Weaving Lab and the Physical Testing Lab as well as the Senior Design Lab and the polymer and color chemistry facilities.

We started with testing the tensile strength, which is the maximum force a fabric can withstand before breaking, and biodegradation of the three polymers’ yarn forms. We then wove the yarn into fabric and conducted testing methods such as abrasion resistance and breaking strength. These tests show that the three polymers are promising options.
Team 10: HighSpeed Moisture Transfer
Sponsor: U.S. Army Combat Capabilities Development Command (DEVCOM)
Team members:
- Erica Lally (Textile Technology)
- Olivia Hensley (Textile Technology)
- Elizabeth Redvanly (Textile Engineering)
- Carson Jenkins (Textile Technology)

What was your challenge/prompt from your sponsor?
Our challenge was to improve the moisture wicking ability (how certain fabrics stay dry by evaporating moisture off of the top layer of fabric) of the base layer of U.S. Army uniforms by 20% compared to the current Army standard.
What solution or end product did you come up with?
We focused on increasing the wicking efficiency of the garment by 20% while also making sure to maintain comfort and remain Berry Compliant, which is the Army standard to keep manufacturing within the U.S.
From the beginning, we knew we wanted to incorporate wool as it has great wicking properties and could help keep the wearer warm. With the consideration of no-melt-no-drip or flame resistance requirements, we went back and forth with the amount of synthetic fiber used in the garment. The current base layer that is worn by soldiers is made of 100% polyester.

After a lot of trial and error and testing of different materials, we decided to use a combination 90/10 wool/nylon blend with extruded polyester. The garment will be a single jersey fabric. The interior of the channel will have a wool base and polyester channel, while the exterior side will be the opposite — polyester base and wool channels. These channels will allow for moisture and sweat to wick towards the sides and “exit” areas of the garment.
What was your favorite thing/most interesting thing you learned about your subject area?
Getting to learn about the current uniforms worn by the soldiers in the U.S. Army! It was also interesting to learn more about the different properties of various fibers and materials.
Where/how do you think you’ll apply the knowledge/skills you have developed in Senior Design?
The most valuable skill that we have learned from Senior Design is how to work effectively with a team. This class has pushed us to be professionals through the extended team project, leading meetings and using time management to conduct research, prototyping and testing over the semester.
Team 9: Process Optimization of Ghillie Suits
Sponsor: U.S. Army Pine Bluff Arsenal
Team members:
- Christopher James Merkel (Textile Technology)
- Jaela Harris (Textile Technology)
- Lauren Boyd (Textile Engineering)

What was your challenge/prompt from your sponsor?
Our challenge from Pine Bluff Arsenal, a U.S. Army installation in Arkansas, was to optimize the production of ghillie suits. These suits are the camouflage uniforms used in the military. We specifically focused on the head drape component which looks almost like a cape.
What solution or end product did you come up with?
Our testing centered around how the process could improve to increase the efficiency of production and decrease labor costs. We utilized Simio, a simulation program that allowed us to replicate the floor plan of the Pine Bluff Arsenal facilities and run experiments to try and optimize the process. Dr. Joines served as our main helper and guided us in the right direction.

Additionally, we ran sewing trials using a binding foot on a sewing machine, which is a tool that helps keep the sewing needle in place, to try and improve the speed of the machinery itself. We also drafted new manufacturing instructions for the suits at the plant. We were able to get a hold of examples online and around the university to serve as a guide.

We found that refreshing the current instructions will allow individuals with no prior experience to create the ghillie suits more efficiently. Additionally, we decided that purchasing another embroidery machine would be extremely beneficial for optimizing production.
What was your favorite thing/most interesting thing you learned about your subject area?
Our favorite part of the project was getting the opportunity to learn and apply the Simio software. Without this project, we don’t think we would have ever explored this software, but now we have unique knowledge on software that we can carry into the workplace.
Where/how do you think you’ll apply the knowledge/skills you have developed in Senior Design?
We absolutely believe that we will be able to apply the skills learned in Senior Design to our upcoming jobs. While this project focused on a much smaller environment, it helped us gain experience so that we can apply that knowledge into larger projects in the future.
Medical/safety textiles
Team 3: Textile Patient Elevator
Sponsor: Stryker
Team members:
- Powell Braddock (Textile Engineering)
- Jordan Nash (Textile Technology)
- Haley Walker (Textile Technology)

What was your challenge/prompt from your sponsor?
Stryker gave us the challenge of creating a patient elevator out of textiles. The goal was to come up with a way to lift a patient from the ground up to stretcher or bed with an emphasis on medical-grade, disposable textiles.
What solution or end product did you come up with?
We created the Sliding Bar prototype which functions by sliding three thin, strong bars under the natural arches of a patient’s neck, back and knees.

There is a disposable nonwoven sheet that has three bars connected to either side. These bars are then pulled under the patient’s neck, back and knees, while the sheet follows. Once the nonwoven sheet has slid completely beneath the patient, the bars are then connected to a lifting system such as a crane.
What was your favorite thing/most interesting thing you learned about your subject area?
It was interesting learning about the requirements and specifications for textiles used in a medical setting.
Where/how do you think you’ll apply the knowledge/skills you have developed in Senior Design?
Our team spent a lot of time ideating throughout the year to come up with unique and groundbreaking ideas for our prototypes. We will use these ideating techniques to bring fresh ideas to our jobs.
Team 5: Protect and Notify
Sponsor: HanesBrands
Team members:
- Sierra Figuerado (Textile Engineering)
- Talib Patrick (Textile Technology)
- Denisse Sada-Romero (Textile Technology)
- Connie Wong (Textile Technology)

What was your challenge/prompt from your sponsor?
Our sponsor, HanesBrands, challenged us to create a protective garment for school-aged children with a notification device that allows the wearer to send an alert to their parents or guardians.
We narrowed down our scope to focus on developing a fabric for hoodies and sweatshirts with increased levels of protection. We specifically evaluated cut-resistance and abrasion-resistance or how much wear and tear the fabric could withstand without compromising comfort.
What solution or end product did you come up with?
Our team created four different fabrics comprised of cotton, polyester and Dyneema that are all comfortable and have varying amounts of protection. Our four prototypes were core spun yarn interlock knit, plated jersey knit fabric, three-ply yarn interlock knit and a self-stitch interlock knit.

We conducted a variety of tests including an in-class hand comfort survey where we compared the softness of our fabric samples. We also tested the amount of pilling using equipment in the Senior Design Lab and a washer and dryer in the Zeis Textiles Extension Dyeing and Finishing Lab.
What was your favorite thing/most interesting thing you learned about your subject area?
There are constantly trade-offs when balancing protection with comfort, and it is not easy to come up with ideas to optimize these two properties.
Where/how do you think you’ll apply the knowledge/skills you have developed in Senior Design?
We have learned valuable skills applicable to working in industry after graduation such as teamwork, communication, time management and presenting. Our team learned how to effectively conduct research during our ideation process. We also met with various professors and the NC State Police Department to gain a better understanding of our topic.
From our prototyping session, we learned what the product development process entails and observed how our prototypes were made from fibers into a yarn and then fabricated into a knit structure.
Athletic/performance textiles
Team 12: Convection Mapping for Shoe Uppers, Under Armour
Sponsor: Under Armour
Team members:
- Fatima Garcia Corona (Textile Technology)
- Shannon Gill (Textile Engineering)
- Eden Millan (Textile Engineering)
- Isabelle Salzmann (Textile Engineering)

What was your challenge/prompt from your sponsor?
Our challenge was to investigate heat and moisture transfer in footwear uppers (the parts of the shoe that cover the top of the foot) and design an upper optimized for breathability.
What solution or end product did you come up with?
We were able to get our knit upper prototype lasted (put onto a shoe), thanks to Under Armour. We are also presenting data that demonstrates the relationship between air permeability and evaporative resistance in order to help define “breathability”.

What was your favorite thing/most interesting thing you learned about your subject area?
Your feet create ½ a pint of sweat per day!
Where/how do you think you’ll apply the knowledge/skills you have developed in Senior Design?
We will definitely be able to apply the technical skills and knowledge we acquired in our careers and the team building/time management skills in any future endeavors.
Team 6: Project Gamer
Sponsor: HanesBrands
Team members:
- Steven Key (Textile Engineering)
- Aidan Lim (Textile Engineering)
- Jan Ray Jison (Textile Technology)
- Anh Bui (Textile Technology)

What was your challenge/prompt from your sponsor?
Our challenge was to create a performance level gaming garment for both the professional eSports player and the average gamer that is not only comfortable, but also provides posture and wrist support.
What solution or end product did you come up with?
We presented a hoodie that focused on mitigating wrist, hand, neck and back pain, as well as sweating. We integrated a compression sleeve into the hoodie to support the wrists and hands.

Our team also added a pillow insert at the lower back of the hoodie to provide a little bit of lumbar support. Lastly, we included a thinner breathable material at the underarm of the hoodie to decrease sweating and increase breathability.
What was your favorite thing/most interesting thing you learned about your subject area?
One of our favorite things we learned in our subject area was learning how to sew. No one in our team knew how to sew so it was a skill we all had to learn for this project. It turned out to be a fun experience: struggling in the beginning but learning new skills and becoming more knowledgeable by the end.

One of the most interesting and important things we learned was how the design process really worked. Starting from the ideation process, we had to learn to cut down which ones were feasible and doable with the timeline we had. After that we had to prototype those ideas to life and test the materials we were using. All in all, it was beneficial to us to learn how the design process worked.
Where/how do you think you’ll apply the knowledge/skills you have developed in Senior Design?
We can apply the knowledge we gained in Senior Design in any product design role since we now know every step of the design process. We also gained experience in conducting tests per commonly used industry standards.
Sustainable textiles
Team 1: Racing Sail Repurposing
Sponsor: Sail to Shelter
Team members:
- Savannah Strickland (Textile Engineering)
- Navami Prabhu (Textile Engineering)
- Rachel Strawn (Textile Engineering)
- Max Ring (Textile Engineering)

What was your challenge/prompt from your sponsor?
Sail to Shelter, a non-profit organization, is committed to keeping racing sails from piling up in landfills by giving them a second life. Sail racing’s high level of competition means athletes have to dispose of their sails after just a few uses.

To keep up with this demand, over 3 million square yards of sail fabric are produced each year, and 97% of that fabric ends up in landfills. Our team’s task was to repurpose woven polyethylene terephthalate (PET) sails into a product that can be used for humanitarian aid.
What solution or end product did you come up with?
Our final products were a semi-permanent shelter and a stuffed bed. The shelter consists of triangular cuts of sails sewn together then sealed with seam tape and a zipper.

This shelter protects those inside from precipitation and wind and is coated with a fire-resistant compound to provide extra safety. In the time given for this project, we were not able to achieve a 100% air-impermeable seam between sails. However, we created a bed made from stuffing sails together.
Team 4: Solar Harvesting Fabric
Sponsor: Phifer
Team members:
- Parker Baker (Textile Engineering)
- Bruce Anderson (Textile Engineering)

What was your challenge/prompt from your sponsor?
Develop a photovoltaic yarn, or a yarn that can convert light into energy, and process to power a motor for an automated car windshield sunshade.
What solution or end product did you come up with?
We developed a process for fabricating a single photovoltaic yarn. This yarn is capable of outputting 300-400 mV of energy with about .08 micro amps for a package of 4-6 inches long. While this is not a lot on its own, we believe that combining many of these yarns would increase the output and efficiency.

What was your favorite thing/most interesting thing you learned about your subject area?
How different and challenging the project actually was. It was a lot of interdisciplinary engineering and research, since it was basically creating a solar panel but in yarn form.
Where/how do you think you’ll apply the knowledge/skills you have developed in Senior Design?
We will definitely use a lot of the soft skills like how to work in a team, give presentations and interact with shareholders. Outside of the soft skills, we were exposed to a lot of different engineering fields that we can draw inspiration or knowledge from.
Independent Study: Floating Wetland Island
Team member:
- Reid Barnett

What was your challenge/prompt from your sponsor?
My challenge was to develop a floating wetland island using only textile products to remove pollution from degraded waters.
What solution or end product did you come up with?
I designed a novel textile-based floating wetland island that can grow plants on polluted waters to absorb and sequester carbon dioxide, nitrogen and phosphorus. The latter two of these chemicals drive cultural eutrophication, the destruction of aquatic ecosystems and toxic algal blooms.

What was your favorite thing/most interesting thing you learned about your subject area?
The interconnectedness of the ecosystem was very interesting, and finding ways to promote a healthier environment in many ways by only changing one aspect of the system was very intriguing to me.
Where/how do you think you’ll apply the knowledge/skills you have developed in Senior Design?
I am hoping to be an inventor and to develop further technology using my Senior Design research in order to create my flagship product.
I have learned a lot about prototyping and what it takes to bring an idea from concept to reality, which I think will be invaluable no matter what I go on to do.
Apparel textiles
Team 8: No Wash
Sponsor: HanesBrands
Team members:
- Noelle Arpea (Textile Engineering)
- Keith Amboya (Textile Engineering)
- Nenfot Goyol (Textile Technology)
- Shannon Sefton (Textile Engineering)

What was your challenge/prompt from your sponsor?
The challenge given by Hanesbrands and Champion was to extend the time their Powerblend hoodie could be worn before it needs to be washed without compromising the comfort, aesthetic or price point of the existing hoodie.
What solution or end product did you come up with?
Our final prototype was an altered Champion Powerblend hoodie that had an antimicrobial finish, which protects fabric from bacteria and odors, as well as an anti-stain finish, sprayed on the fabric to act on the outside of the garment.

The hoodie also had a breathable underarm panel going from the cuff of the sleeve to the waistband of the body made from a mock mesh material. The mock mesh has better breathability and similar durability compared to the body fabric, and it looks very similar.
Team 11: Digital Yarn Dyeing
Sponsor: Gildan and Twine
Team members:
- Natalie Young (Textile Technology)
- Rachel Drum (Textile Technology)
- Morgan Mase (Textile Engineering)
- Julia More (Textile Engineering)

What was your challenge/prompt from your sponsor?
Our prompt was to design an improved sock prototyping process using the TS-1800 digital yarn dyeing machine from Twine Solutions.
What solution or end product did you come up with?
We were able to quantify the time, yarn and water it took for both the TS-1800 and traditional dye process to color match a single color, that is to replicate exact colors from one material to another. Our research shows how the TS-1800 digital dyeing machine can be a sustainable solution for Gildan.

Additionally, we quantified the machine’s color gamut (how many colors it can produce) abilities based off of Gildan product colors. We listed all of the limitations of the machine — a large one being it can only dye polyester — and we listed the benefits of the machine — a large one being it can dye very unique designs that cannot be achieved with any other machine on the market.

We came up with the final conclusion that the machine has great potential for sustainability gains and unique design applications, and it eventually will be a great investment for Gildan once the machine broadens its color gamut and substrate dyeing capabilities.
What was your favorite thing/most interesting thing you learned about your subject area?
Our team really enjoyed learning about the L*a*b* color space, which is a way of expressing color according to its perceptual lightness and the four colors of human vision. We were also interested in how altering the color formula changes the final result. We enjoyed learning all about dyeing and the color matching process in the dyeing and finishing lab, as well as learning how the sock machine works.
Where/how do you think you’ll apply the knowledge/skills you have developed in Senior Design?
Working with both our sponsor, Gildan, and the Twine Solutions team has given us insight into the “corporate world” and how communication is very important for success when working with a larger team of people from different backgrounds.
Coordination within Wilson College was also a learning experience because we had to plan ahead to make sure we could get into the labs that we needed at a time that would keep our project on track. Working in our team of four was also a great experience because we could apply our unique skills to the advantage of the team, and it was really fun getting to know everyone!
Independent Study: Wireless Charging
Team member:
- Ethan Hill

What was your challenge/prompt from your sponsor?
My challenge was to combine the utility of wireless charging with textile comfort by integrating inductive coils into textile garments.
What solution or end product did you come up with?
I developed a wireless charging receiving garment. By turning on the battery sharing functionality, a user can power wearable electronics from their pocket. Picture having pants that charge your earbuds when you place your phone in one pocket and the charging case in the other. Additionally, consider having a shirt that powers medical implants by acting as both a receiver and transmitter, all powered by placing your phone in your pocket without plugging in your phone.

My project addresses these end uses with a coil that is embroidered onto fabric and placed into a pocket. My main deliverables include an engineered coil design that is secured to weft-knit open mesh and covered by a nylon-spandex compressive layer. The two fabrics hold the coil against the phone in the pocket, ensuring that the wireless charging connection is not interrupted while the user is performing daily activities.
What was your favorite thing/most interesting thing you learned about your subject area?
I learned that getting two coils to resonate (transfer the most power) is similar to tuning a string instrument. Induction coils require a function generator and dial to connect to an oscilloscope, whereas a violin has a peg to tune a string. Similar to how the different thicknesses of a violin’s strings produce varying sounds, a coil’s diameter size determines how it will resonate.
Where/how do you think you’ll apply the knowledge/skills you have developed in Senior Design?
I have been able to apply methodologies learned in this class with personal projects. I have also become a more proactive student, in that I have the confidence to discuss technical information with my professors and peers. For example, talking to employers about my experiences has become far easier due to meetings with the standard review board, which is a group of professionals who review our project.

Senior Design has taught me the importance of simplifying complex topics into digestible and concise information. Because of Senior Design, I feel confident in the work that I produce as an engineer and feel that I have deliverable skills that I can demonstrate to employers.
- Categories: