Dream Job: Sustainable Textiles
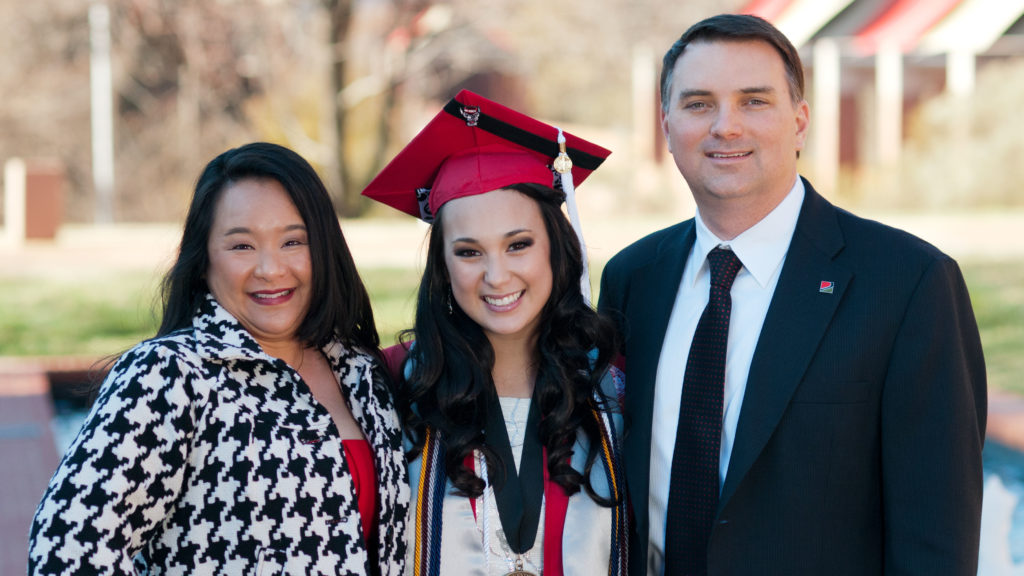
A second generation alumna of the Wilson College of Textiles, Cassia Lewis practically grew up at NC State, biking around campus and cheering on the Wolfpack at football games with her father, who graduated from the Textile Engineering program in 1994. She now lives on the West Coast, serving as director of business development for fabric manufacturer Swisstex Direct.
She graduated in 2013 with a B.S. in Fashion and Textile Management (with a concentration in product development). Swisstex is a circular knit manufacturer with facilities in Los Angeles, California and El Salvador. Its clients include New Balance, Puma, Under Armour, HanesBrands, Reebok and more.
“We are an extremely sustainable dye house and finishing facility,” she said. “Honestly, that’s what sold me on moving to Swisstex. I took a tour through the entire facility and it’s really state of the art; there’s not another textile facility I know of that can compare. We’ve done a lot of significant investment in the type of machinery and the way things are run. That Swiss ownership and mentality — it’s a very efficient mentality, but they are also heavily invested in having us as sustainable as possible, with the least impact on the planet.”
According to Lewis, the company is the only dye house in California that uses a thermal oxidizer, which uses high temperatures to render safe hazardous gases.
“Additionally, we are known across the industry for our water usage — or actually the lack of water usage, I should say. Most textile mills across the globe use about 20 gallons of water per pound that they process,” she said. “We are a bluesign® system partner, which is kind of an industry standard for chemicals in the market…Most bluesign® mills use seven gallons of water per pound; we actually use about three gallons per pound, so we’ve been very proud of our efforts to reduce water usage.”
If the name Swisstex makes you think of a well-calibrated watch, it is for good reason. According to Lewis, their automated dye house runs like a chronograph.
“Our color system actually uses a pipette robot to pull the exact increments of the different dyes to create lab dips — and it does it in an extremely quick time,” she said. “Where most mills can only process 25, maybe 30 lab dips per day, we can do up to 300 with the automatic machine.”
Lewis takes pride in working for a company that she feels is on the leading edge of sustainability.
“It’s so exciting to see that in our industry, which is the second most polluting industry on the planet, we are making an effort to meet sustainability goals,” she said. “The brands we work with are targeting to have all products in their lines recycled or organic or somehow sustainable by 2024, 2025. It’s great to see this shift in the industry, to target and innovate around sustainability, and that’s very much what we’re working on here at Swisstex.”
Note: This is a portion of the full article, which is written by Cameron Walker and appears on the Wilson College of Textiles website.